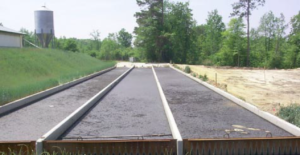
Settling basins are long, shallow structures using gravity to settle solids.
Livestock and poultry producers are seeking alternative treatments for animal manure and process-generated wastewater to reduce excessive nutrient loading and odor potential of liquid manure storage structures.
Solid-liquid separation is the partial removal of organic and inorganic solids from a mixture of animal manure, open-lot runoff and process-generated wastewater, also known as liquid manure. Liquid manure systems are popular among livestock and poultry operations because they make manure easy to handle, store, treat biologically in lagoons and land apply. The manure pits and gutters also are easy to recharge and flush using lagoon liquid.
Separated solids may be used for composting, refeeding or generating biogas (methane). The composted material can be used as bedding in free stall barns. Separating the solids from the liquid manure makes the liquids easier to pump and handle. It also helps reduce:
- The amount of organic material (organic loading)
in treatment lagoons - Odors in storage and treatment facilities
- Build-up of solids in primary lagoons
- Frequency of lagoon sludge removal
- Potential surface and groundwater pollution, because less nitrogen, phosphorus and other constituents are in the separated liquid
Separation techniques and equipment
The main objectives of solid-liquid separation are to physically separate and remove the suspended solids and some of the dissolved solids from the liquid manure. Several methods are available to separate solids from liquids:
- Sedimentation (solids settle by gravity).
- Mechanical separation. Gravity and mechanical separation are the two most common techniques used for this purpose.
- Evaporation ponds. These may be effective in arid regions where much more water is removed by evaporation than is added by precipitation. Compared to systems that use treatment and irrigation of effluent, the use of these ponds is limited by their larger size, design requirements and current and evolving environmental regulations.
- Dehydration. This method, which uses heat to remove moisture, is unpopular because of its high initial costs, maintenance and energy requirements.
- Coagulation Flocculation. A relatively new technique for solid-liquid separation uses chemicals to aggregate suspended solids (coagulation) to form settleable particles and to convert particles into large, rapidly settling flocs (flocculation).
Sedimentation
Settling basins are structures designed to separate solids from liquid manure by sedimentation. The inflow of manure is restricted to allow some of the solids to settle out. The liquids and some solids gradually drain to a holding pond, a treatment lagoon or to some other storage structure. Solids remaining in the basin are left to dry and then are removed.
Settling basins should be shallow (typically 1 to 3 feet deep), long, wide and free-draining. Flow velocity at the design flow rate should be less than 1 foot per second; a hydraulic retention time (average retention time for liquid manure flowing into the basin) of 20 to 30 minutes is desired.
Mechanical separators
The types of mechanical separators include screen separators, centrifuges, hydrocyclones and presses (screw or belt type).
Screen separators
The separators are further classified as stationary, rotating and vibrating screens.
Stationary inclined screen: These so-called static screens use gravity to separate the liquid manure from the solids. Liquid manure is pumped to the top edge of a screen. Liquids pass through the screen, while solids accumulate and slide down the screen to be deposited on a collection pad or auger. This type of screen separator is widely used to remove fibrous, coarse particles from dairy manure, which makes it easier to handle, store and treat the manure, recycle the liquids for flushing, and apply them to the land.
The advantages of such screens are that they have no moving parts and require little power. However, they need a separate wash-down system to keep the screen from clogging. They also require a sump and pump to collect liquid manure and induce flow over the screen.
In-channel flighted conveyor screen: This separator consists of an inclined screen and a series of horizontal bars called flighted conveyors. The separator can be placed directly into an open wastewater channel, which eliminates the need for a sump or a pit and a lift pump. A chain drags the flighted conveyors carrying liquid manure over the top of the inclined screen. The liquid passes through the screen and drains into the channel on the downstream side of the separator, while the separated solids are deposited on a collection pad. The uses for these separators are similar to those of stationary inclined screen separators, but the conveyor screen separators require more mechanical maintenance because their moving parts are exposed to corrosive and abrasive materials.
Vibrating screen separator: This separator has a screen that vibrates rapidly, which helps keep the screen from excessive clogging. Liquid manure is pumped onto the screen at a controlled rate. The liquid passes through the screen and is collected into a container underneath it. The separated solids remaining on the screen move to the screen edges.
Rotating screen separator: As the name suggests, a continuously turning or rotating screen, similar to a clothes dryer, receives liquid manure at a controlled rate. A scraper removes the solids that collect on the screen; the liquid passing through the screen is collected in a tank.
Centrifuges and hydrocyclones
Centrifuges and hydrocyclones separate solids from liquid using centrifugal force to increase the settling velocity of suspended particles. Vertical and horizontal centrifuges have been used in food processing and industrial waste management operations. Livestock producers have used them to separate manure solids.

Settling basins are long, shallow structures using gravity to settle solids.
One type of horizontal centrifuge uses a rotating cylinder. As liquid manure enters the cylinder, solids are separated from the liquid. An auger inside the cylinder, turning faster than the cylinder, moves the solids to an opening on one end, where they are discharged into a stack or container. The liquid is discharged from the opposite end. Hydrocyclones are cone-shaped cyclone separators that have no moving parts. A hydrocyclone is configured so that when liquid manure is pumped at an angle into the cyclone near the top, it swirls at a high speed. The strong swirling motion separates the solids by pushing them outward, and they settle by gravity at the bottom of the cone. The liquid exits from the top of the cone through a pipe. These separators require booster pumps at 30 psi or more.
Presses
The separated solids resulting from sedimentation, screening and centrifuging are referred to as solid cake, which can contain as much as 85 to 95 percent moisture (only 5 to 15 percent total solids). Presses are used to remove more water from the solid cake, so that it can be composted or fed to livestock. Types of presses include roller presses, belt presses and screw presses. These devices help remove fine-textured particles.
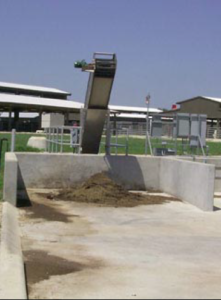
The discharge end of an in-channel flighted conveyor separator.
- A roller press has concave screens and a series of rollers and brushes that press liquid manure against the screens. The liquids are squeezed out and the solids remain on the screen.
- A belt press uses a flat fabric belt, which runs horizontally between rollers. The rollers squeeze the liquid manure through perforations in the belt, which retains the solids.
- A screw press uses a cylindrical screen with a screw-type conveyor in the center. The screw conveys the solids retained on the screen to the discharge end for solids. The screw conveyor also
compacts and removes water from these solids during transport.
Chemical treatment
Researchers are studying the processes of coagulation and flocculation of particles, which use chemicals to help separate solids from liquids in animal manure. Coagulation is a process of gathering solids that are suspended in a liquid into a mass to form particles that can settle. Flocculation is a process that converts coagulated particles into large, rapidly settling masses, also called flocs.
The most common chemicals used to coagulate and flocculate solids in animal manure and wastewater are organic polymers such as polyacrylamide (PAM), and metal salts such as ferric chloride (FeCL3), alum (Al2(SO4)3) and lime (Ca(OH)2). These chemical treatments may work well for manure with fine particles, such as poultry and swine manure.
Laboratory studies have found that ferric chloride and alum are effective coagulants that help manure solids to gravity settle by sedimentation. A polymer used with ferric chloride or alum produces dense flocs and helps remove solids by the process of screening.
Performance and economics of separators
Each kind of separator works best in certain types of livestock operations. One measure of the ability of a separator to work well in a certain operation is the separation efficiency, which is the percentage of total solids removed from liquid manure. Each system is designed to separate a range of particle sizes; its efficiency depends on the flow rate of the manure, the shape and size distribution of the particles, and their chemical nature. When you are considering solidliquid separation systems for your operation, base your choice on the type and volume of liquid manure and wastewater that your operation generates.
Some separation systems are ineffective when used alone in some types of operations. Sedimentation and mechanical separation systems have low separation efficiencies. Neither system effectively removes finer solids (less than 0.25 mm or 0.01 inch in diameter), which can create a number of odor-producing compounds when carbohydrates, proteins and fats decompose anaerobically (without free oxygen). These finer solids also contain nutrients such as nitrogen and phosphorus. Therefore, sedimentation or mechanical separation alone may not significantly reduce odors or nutrients from manure and wastewater.
Sedimentation
When designing a sedimentation basin, the primary factors to consider are the manure and wastewater flow rate, the solids settling rate and the detention time (time between inflow and outflow of liquid manure). Studies show that sedimentation seems to be most effective for treating highly diluted manure and wastewater (flushed manure or feedlot runoff) consisting of less than 3 percent total solids. Generally, settling is reduced if the manure is more than 1 percent suspended solids.
The separation efficiency for sedimentation basins (total solids removed) has been reported as high as 64 percent for a concrete swine feed lot and 39 to 75 percent for an earthen beef feed lot. In the latter case, much of the solids load consists of relatively large soil particles detached from the corral surface during rainfall.
Researchers tested the performance of a settling basin having two compartments (3 feet deep and 80 feet long each) operated in parallel for an open lot dairy in Erath County, Texas. All process-generated wastewater from the milking parlor and drip shed, as well as any rainfall runoff from the lots, were channeled into the settling basin. The overflow from the settling basin was directed to an anaerobic treatment/ storage lagoon. The settling basin provided a separation efficiency of 33 percent for the total solids and 45 percent for the volatile solids.
Mechanical separators
Field tests have been conducted on the separation efficiencies of different types and brands of mechanical separators. The performance of those different mechanical separators has varied widely. Efficiencies ranged from 3 to 67 percent of total solids removed, depending on the screen size (openings), the type of manure and the flow rates used. In addition, manufacturers claims may also be based on total suspended solids or volumetric percent solids determined using Imhoff cone (a cone-shaped graduated vessel to measure settleable solids). The test results may be misleading if they are not based on total solids or volatile solids.
When checking the results of such tests, be sure that the report includes accurate information about such variables as the type of liquid manure tested (swine, beef or poultry), the total solids content in the raw manure before testing and, where applicable, the liquid flow rate entering the separation system.
The performance of screen separators depends on the size of the screen opening, the flow rate of liquid manure and manure characteristics such as solids content and particle size distribution. Studies show that screens perform much better with manures containing less than 5 percent solids. Higher flow rates and solids content tend to clog screen openings, causing more water to accumulate on the screen surfaces and more moisture remaining in the solids.
Presses and centrifuges have higher separation efficiencies than screens and produce relatively drier solids. Little performance data are available on presses and cyclones. At a dairy milking center at Erath County in Texas, a hydrocyclone solids separation system reduced the total solids concentration in the wastewater outflow (flow exiting the separator) by 34 percent as compared to that in the inflow (flow entering the separator).
Chemical treatment
Laboratories have tested how well chemicals help separate solids in animal manure by coagulation and flocculation, but there is no standard method for testing in the field. Some bench scale studies have shown that many more total solids are removed when sedimentation or mechanical separation is followed by chemical treatment of liquid manure. Researchers are working to establish the optimum dosing (i.e. continuous feed) for these chemicals.
Economics
The costs involved in separating solids from liquid manure, process-generated wastewater and open-lot runoff include the cost of the separating system, construction and/or installation, energy and labor to operate the system, and system maintenance and repairs. Mechanical separators range from $10,000 to more than $50,000, not including the cost of pumps, sumps and channels. Their throughput capacities (the amount of liquid manure and wastewater processed) vary from 100 to 600 gallons per minute.
For the same capacity, screens cost less than centrifuges or presses. Some manufacturers provide options to install presses on a screen separator to remove more water from the separated solids. When selecting the separation method and equipment for a particular manure management system, consider the amount of manure and process-generated waste to be treated, the objective of solid-liquid separation and the planned use of the separated solids.
For more information
Auvermann, B. W. and J. M. Sweeten. 1992. Evaluation of Hydrocyclone Solids Separator for Dairy Manure. Erath County Field Day Report. Texas Agricultural Extension Service, Texas A&M
University System.
Midwest Plan Service (MWPS). 1993. Livestock Waste Facilities Handbook. MWPS-18. MWPS, Iowa State University, Ames, IA 50011.
Sweeten, John M. and M. L. Wolfe. 1993. The Expanding Dairy Industry: Impact on Ground Water Quality and Quantity with Emphasis on Waste Management System Evaluation for Open Lot Dairies. Tech. Report No. 155. Texas Water Resources Institute. Texas A&M University, College Station, TX 77843-2118.
Zhang, R. H. and P. W. Westerman. 1997. Solid-liquid separation of animal waste for odor control and nutrient management. Applied Engineering in Agriculture 13(5):657-664.
Original article by Saqib Mukhtar, John M. Sweeten and Brent W. Auvermann*
Produced by Agricultural Communications, The Texas A&M University System