Continued growths in number of milking cows, milk productivity per cow and number of concentrated animal feeding operations (CAFO) are all leading to increases in quantity and concentration of manure. Under these conditions, poor manure management practices coupled with uncertainty in rain events pose a greater threat to the health of surrounding ecosystems, in addition to the economic loss of manure nutrients as runoff. This study presents a comprehensive model of granulation as an advanced processing alternative for dairy manure. Granulation offers an opportunity to improve manure characteristics, which facilitate precise land application and affordable transportation. Additionally, it could improve manure acceptability as organic fertilizer thus adding a revenue source to producers. The impacts of herd size, management practices, operating costs, and internal rate of return (IRR) on the minimum sale price (MSP) of granulated manure were quantified. Herd size was found to significantly impact MSP for herds below 10,000 cows. For herds of 1,000, 5,000 and 10,000 cows, the MSP were $559, $291, and $237 per metric ton of granulated manure. The process economics were evaluated in terms of breakeven distances, which correspond to transportation distances at which the cost of granulation equals the savings in transportation cost. Finally, process economics were evaluated in terms of unit mass of phosphorus (P) retained in the granulated manure. When considered as a technique to export P off eutrophic watersheds for sale as organic fertilizer, granulation may be competitive with other P-reduction technologies.
Introduction
Manure management is increasingly becoming a challenge to livestock producers. Competition for crop fields and pasture land in regions of concentrated livestock production has led to increased costs, mainly due to increases in manure hauling distances. Manure-related water quality degradation has resulted in tighter regulations of manure application (Ribaudo et al., 2003). Projected increases in global demand for livestock products, i.e., milk, meat, and eggs will be likely met by expansion of existing farms, or the establishment of concentrated livestock feeding operations (CAFO), thus increasing manure impacts on surrounding ecosystems (Thornton et al., 2010).
Various technologies are available to assist livestock producers in managing manure sustainably. Manure liquid-solid separation, using screen separators, screw presses, and centrifuges, facilitates precise manure application to match crop needs. It also enables producers to store and transport more nutrients, in the solid-rich fraction, for the cost of acquiring and operating the separation system. Advanced processing technologies, such as composting, combustion, pelletization, and granulation all result in a condensed, solids-rich manure fraction, i.e., compost, char, pellets and granules, respectively. Manure granulation is a promising technology for nutrients densification as it requires less energy inputs when compared to pelletization. Unlike combustion and composting, granulation does not significantly alter manure composition or result in significant loss of manure nitrogen (N) and carbon (C).
The goal of this study is to present a modeling tool to evaluate the economic performance of the granulation process as a manure management alternative to dairy producers. We present a model that evaluates the impact of endogenous factors: herd size, separation technology, as well as exogenous factors.
Materials and Methods
The following sections present the components of the technical/economic assessment for the manure granulation system.
Herd size and manure production
The size of the dairy herd (number of cows) is the main driver for the technical/economic modeling routine. While dairy herds typically consist of cows at different life age, i.e., calves, heifers, lactating and dry cows, this study considered herds composed strictly of lactating cows. This choice was made to facilitate interpretation of the results regardless of the herd structure. Manure rate and composition for lactating cows was based on ASABE D384.2 standard.
Given that the technology investigated here, granulation, presupposes a surplus of manure, the smallest herd size considered is a 1,000 lactating-cow herd. To date, the largest dairy farm in the U.S. has more than 30,000 cows. In our model, we chose to simulate herd sizes up to 50,000 cows to provide an estimate for the cost of this technology which accounts for future size increases, as well as for potential central processing of the manure from different mid- and large size dairy operations.
On-farm manure management
The choice of dairy manure management system, in terms of collection (scrape/flush), processing (liquid-solid separation), and stabilization (anaerobic digestion/composting) determines the quantity and composition of manure available for further processing. Variability between management systems and differences in operational conditions within similar systems render the choice to model a single or few systems a limitation of this analysis. Therefore, on-farm management decisions were treated as a “black box” block that is characterized only by the yield of outgoing manure (output) as a percentage of as-excreted manure (input). Similarly, yields of total solids, volatile solids, nitrogen (N), phosphorus (P), and potassium (K) after on-farm management were used to characterize on-farm manure management. These yields could be easily adjusted to represent a specific farm management scenario, e.g., a flush-system followed by anaerobic digestion. This representation also allows for accounting of the volatilization losses (N and C) that vary with different management choices. The parameters presented here represent data compiled from an inventory of a dairy farm (4,000 heads) in Manitowoc County, Wisconsin. This farm employs a flush system that uses recycled manure liquid, followed by an anaerobic digester that supplies biogas to generate on-farm power requirements with the surplus power sold to the grid. The sludge-rich stream, which typically retains most nutrients, was selected as the raw input to the granulation process.
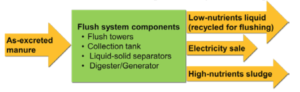
Fig 1. Schematic flowchart of a flush system on a dairy farm and its outputs
Granulation system layout
The granulation system modeled in this study, shown in Figure 2, can be divided into the following steps:
- Dewatering
- Homogenization
- Granulation
- Drying
- Screening/partial recycling
Dewatering involves the removal of free water from the dairy manure sludge. This step is typically accomplished using a liquid-solid separator on manure streams at between 3 and 10% total solids. In this study, two different liquid-solid separators were evaluated, i.e., screw press and decanter centrifuge. The separation efficiency for each separator was based on published literature on their performance. Purchase price and energy consumption for each unit were also determined to evaluate the share of capital and utility costs associated with this step. The concentration of solids in the solid-rich fraction leaving this step was 25% for both units. However, N and P levels in solid fractions corresponded to the respective separation efficiency of the separator selected.
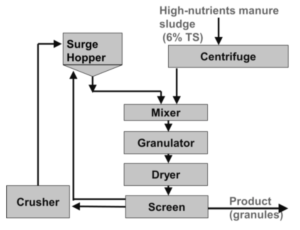
Figure 2. Schematic diagram of manure granulation system
Dewatered manure was fed into the mixer, along with recycled fine dry manure particles, to create a homogenized mixture, at around 40% total solids, suitable for granulation. The mixing stage was modeled as a horizontal paddle-mixer with two shafts. The homogenized mixture was then transferred to a disc granulator where an inclined rotating pan facilitates the nucleation and growth of uniformly-shaped spherical granules. Granules diameter was controlled by changing the feed rate per per batch and/or the rotational speed of the disc. The granulated dairy manure was then fed into a rotary dryer to bring the moisture content to 10%. In addition to moisture loss, a share of the inorganic nitrogen and organic matter (OM) are typically devolatilized. Accordingly, these losses were included in the model. The thermal energy requirement for the drying process was based on moisture contents of incoming and outgoing streams and the drying efficiency for rotary dryers. Actual granulation tests were conducted on a pilot-scale granulation system, with the same configuration shown in Figure 2, using manure sludge from the same dairy farm. N and OM loss, as well as dryer efficiency used in this model were based on the results of these pilot-scale tests.
Economic model of granulation system facility
To study the impacts of herd size and manure management practices on the economics of granulating dairy manure solids, complete accounting of costs associated with the granulation facility was performed. Net present value (NPV) analysis of the granulation project, at different herd sizes, was carried out to evaluate the economic performance of this process. This analysis methodology determines the sum of net cash flow, in current dollars, over the entire project life. The following sections detail the various cost components associated with this project.
Initial investment
The capital cost for this facility covered the direct cost, which included equipment purchase, installation, electrical facilities, and buildings, in addition to the indirect capital cost that covers engineering and contractor fees, and a contingency expenditure. The total initial investment committed to the project typically includes the direct and indirect capital costs detailed above, in addition to startup and validation costs, and a working capital that covers the operation expenditure for 30 days. Estimation of these various cost items, except for the working capital, is typically based on the freight on board (FOB) purchase price of the equipment and using ratio factors for total capital cost approximation. The direct capital cost of a granulation system to process manure solids originating from a 15,000-head herd, solicited from an equipment vendor, was $3.9 million (2015 U.S. dollars). A capacity factor of 0.6 was used to estimate the total investment associated with granulation systems sized for different herd sizes from the quoted installed cost.
Product costs
Operating costs included raw material and consumables cost, labor wages, utility cost (heat and electricity), in addition to maintenance and insurance costs. Given that this analysis is predicated on a situation where dairy manure is considered a nuisance (i.e., waste), no costs were associated with the acquisition of the manure. Similarly, no consumables use was modeled for this system. The model assumes the facility operates 12 hours a day, 7 days a week, with an annual down-time of 2 weeks for maintenance and repairs. The labor needs of this facility were estimated to be met by 3 full-time operators, and were held fixed for all facility sizes. Estimates of the electrical power and thermal load associated with this system were based on estimates provided by the vendor. The thermal load, associated with the drying step, were verified using calculations of initial and final moisture content, as well as dryer efficiency. The utility consumption was assumed to scale linearly for the various facility sizes, i.e., scale factor = 1 .The project life was assumed to be 15 years, with a salvage value for the facility equal to 5% of the direct capital cost. Capital investment was amortized using straight-line depreciation. A marginal federal tax rate of 37%, and no state tax, were assumed in this study. An annual inflation rate of 2% was used to calculate the labor, energy, and sale price over the project life.
Sale revenue
The only cash revenue in this project was realized through sale of the granulated manure solids. Accordingly, the model was constructed to calculate the minimum sale price of 1 metric ton (Mt) of granulated manure. The minimum sale price was taken to be that which results in a net zero present value for the investment (NPV=0) (Short et al., 1995). This present value marks the hurdle level this technology must at least overcome in order to yield an internal rate or return (IRR) equal to the relevant discount factor. Three different discount factors (4%, 8%, and 10%) were used in this study to test the sensitivity of the minimum sale price of the granulated manure to the chosen discount factor.
Results and Discussion
The granulation process offered flexibility to dairy producers by capturing 20% of as-excreted N, 60% of as-excreted P, and 22% of as-excreted K in a granulated form that weighs 5% of total as-excreted manure. Process economics was sensitive to the farm size, and could be significantly costly to small farms. The phosphorus captured in the granulated manure offered an opportunity as a P removal strategy in eutrophic watersheds.
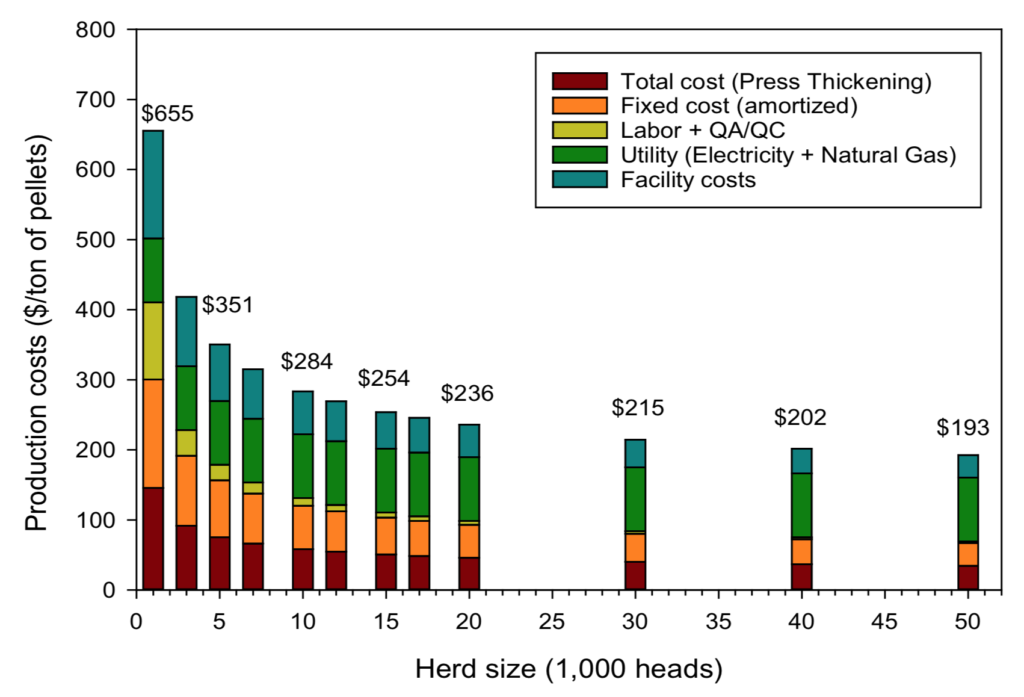
Fig 3. The effect of herd size on the cost of granulation
Conclusions
- Despite the increased cost of thickening using a centrifuge,, the total pelletization cost becomes lower than using a screw press unit
- As farm size increases, the pelletization main cost component becomes electricity and natural gas costs ($$995//MMt)
- Pelletization only marginally reduces transportation cost (i.e., extremely large transportation distance is needed to offset processing cost)
- Pelletization at sufficiently large facilities (~110K heads) can be a useful P – concentration and transportation technique
- Cooperative pelletization in dairy – rich watersheds could be a solution to adopt this technology as P – reduction measure
References
Ribaudo, M., Kaplan, J. D., Christensen, L. A., Gollehon, N., Johansson, R., Breneman, V. E., … Peters, M. (2003). Manure Management for Water Quality Costs to Animal Feeding Operations of Applying Manure Nutrients to Land. SSRN Electronic Journal. http://doi.org/10.2139/ssrn.757884
Thornton, P. K., Audsley, E., Brander, M., Chatterton, J., Murphy-Bokern, D., Webster, C., … Bank, W. (2010). Livestock production: recent trends, future prospects. Philosophical Transactions of the Royal Society of London. Series B, Biological Sciences, 365(1554), 2853–67. http://doi.org/10.1098/rstb.2010.0134
Original article by Mahmoud A. Sharara, Qiang Yang, Tom L. Cox, and Troy Runge