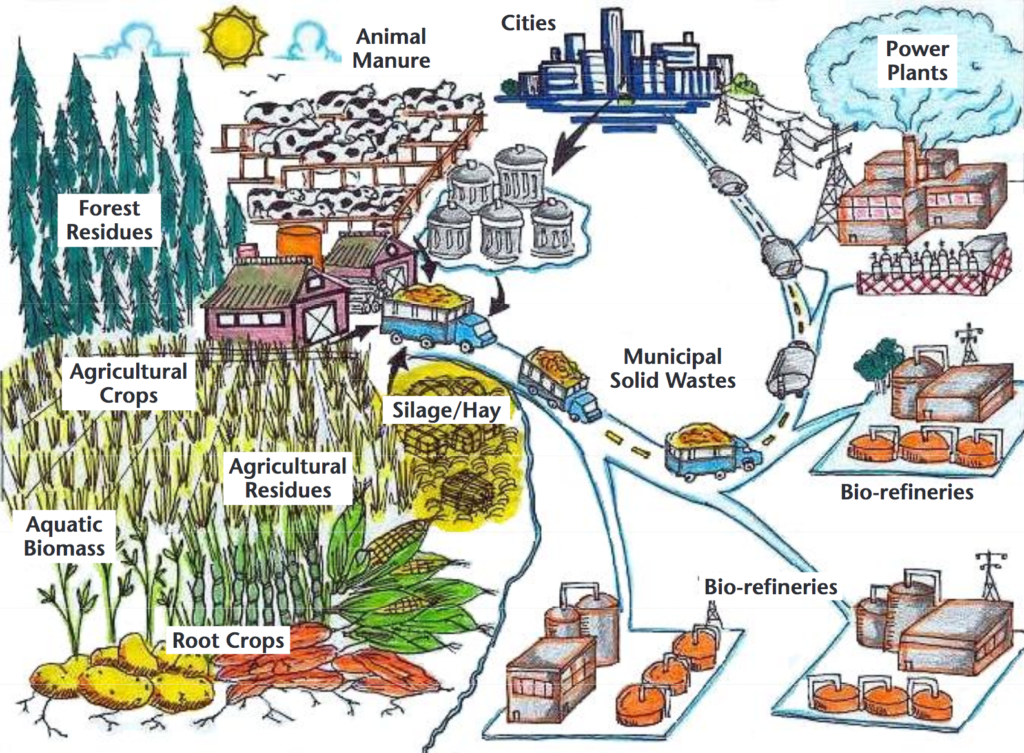
Figure 1: Future of agriculture: supply of food fiber and bio-fuels.
Today the spotlight in the United States is on the increasing world demand for energy and the high cost of oil and natural gas. This has heightened interest in alternative and renewable energy sources, such as bio fuels, forests, wind, solar and animal manure.
While demand for hydrocarbon energy (energy from crude oil, natural gas and coal) will continue to rise, renewable energy will become more important in the coming years.
This publication uses the following figure as a simple illustration of potential sources of energy from biomass, including trees, agricultural crops, animal manure and municipal solid waste. The biomass will be field-harvested, preprocessed and transported to bio-refineries for treatment and processing. It then will be converted to bio-fuel for transportation, industrial chemicals or power plants to supply electrical power for public consumption.
Efforts are under way at the grassroots level by America’s farm, business and labor leaders, and conservation groups to obtain 25 percent of the total energy consumed from U.S. croplands, forests and farms by 2025. This movement, which is called the 25 X 25, includes animal feeding operations. It is gaining widespread private and public support.
Energy from Feed to Manure
Manure containing undigested and partially digested dietary nutrients is a resource that benefits plant growth and adds organic matter to improve soil structure. Nutrients in animal feed that are sources of energy include carbohydrates — comprised of carbon (C), hydrogen (H) and oxygen (O) — from forage and cereal grains, for example. Other nutrients are proteins (in the form of amino acids) and fats (or lipids), comprised primarily of C, H, O as well as phosphorus (P) and Nitrogen (N).
The energy content of animal feed is expressed in calories. One calorie is the quantity of heat required to raise the temperature of one gram of water by 1 degree Celsius (°C) from a standard initial temperature and pressure at sea level. Not all of the energy in the feed is utilized by the animal.
The energy in feed can be portioned into net energy and lost energy. Energy losses during the digestion process include the energy lost in manure (feces and urine), in gases produced by fermentation in the gastrointestinal (digestive) tract of animals and through heat. Several processes have the potential to transform the energy in manure to usable bio-energy.
Important Manure Properties in the Conversion to Energy
Besides the processes and principles involved in manure and biomass conversion to energy, familiarization with the following terms will help consumers understand the scientific jargon of bio-energy production:
- High and Low Heating Values. High heating value (HHV), a measure of biomass energy (BTU per mass or volume of manure, etc.) results from combustion of samples using a calorimeter. These values can also be calculated by formulae using the ultimate analysis of biomass. A low heating value (LHV) is the correction to HHV due to moisture in the fuel (biomass) or water vapor formed during combustion of hydrogen in the fuel.
- Proximate Analysis. The proximate analysis is a good initial indicator of biomass (manure) quality. Biomass samples are analyzed to determine the moisture content, ash and volatile matter (solid material in biomass that, when heated at a specific temperature, converts directly into the gaseous phase without undergoing a liquid phase). Proximate analysis also determines fixed carbon, which is calculated by subtracting moisture, ash and volatile matter from the total biomass.
- Ultimate Analysis. Ultimate analysis reports the percentage of C, H, O, S and N in the biomass. The values of these elements may differ by types of animal manure or other biomass types. The ultimate analyses can determine the heating value of biomass fuels. The amount of S and N in biomass, including manure, helps determine the design and operation parameters of a bio energy-producing system by the different thermo-chemical processes.
The heating value of manure on a dry ash free basis (DAF) is estimated at 8,500 Btu/lb, according to extensive field research by the Texas Agricultural Experiment Station and Texas Cooperative Extension. When manure is to be converted to energy, this heating value is considered the input energy into the conversion process. To generate useful energy and fuel, manure could be converted through the action of microorganisms for the production of methane (biological process) or through the action of heat at high temperature with or without the presence of air or oxidant (a thermo-chemical process).
Biological Process
Methane production is the biological process that generates energy from animal manure. The process, which is called anaerobic digestion, is the treatment of manure with naturally occurring microorganisms (bacteria) in the absence of air (especially oxygen) to produce biogas.
Biogas, which is produced from degradation of organic matter in manure by the bacteria, contains primarily methane (CH4) and carbon dioxide (CO2). Other gases, such as nitrogen (N2), hydrogen sulfide (H2S) and trace organic components are also present in relatively small quantities. Typically, 60-65 percent of the biogas is CH4. Methane and CO2 represent more than 90 percent of the biogas. Virtually all N, phosphorus (P) and potassium (K) remain in the digested manure.
Methane produced from anaerobic digestion and utilized as a source of energy also reduces its natural emission, which has much greater global warming potential than CO2. The heating value (energy released from a given mass of a fuel of biogas containing 65 percent CH4) is approximately 600 BTU/ft3.
The British Thermal Unit (BTU) is the heat required to raise the temperature of one pound of water by one degree Fahrenheit (°F). There are 252 calories per BTU. For comparison, 1,000 ft3 of biogas with 65 percent CH4 will be an approximate equivalent of 600 ft3 of natural gas, 6.6 gal of propane and 4.7 gal of gasoline.
Information on types of biogas digesters and their function is available from the USEPA website at www.epa.gov/agstar.
Thermo-chemical Process
Thermo-chemical processes include direct combustion, co-firing, gasification and pyrolysis. Direct combustion refers to burning biomass directly in a furnace to produce heat and electricity. Steam produced from heat of combustion powers a turbine that turns a generator to produce electricity. Manure as a fuel has the potential to be burned directly. However, because its ash content (the inorganic residue, such as soil or other inorganic material, that remains after combustion) is higher than other biomass (e.g., wood and straw) or fossil fuels (e.g., coal), direct combustion of manure is not practical and efficient.
Because of the variability of animal manure, it is often desirable to mix it with other less variable fuels for combustion. One means of doing this is co-firing, which refers to mixing biomass and fossil fuels in conventional power plants. Significant reductions in emissions from sulfur dioxide (SO2) — an air pollutant released when coal is burned) — are achieved with co-firing systems in power plants that use coal as input fuel.
Small-scale studies at Texas A&M University show that co-firing of manure with coal may also reduce emissions from coal of nitrogen oxide (NOx), which contributes to air pollution. This depends whether the manure is injected at the proper location, such as the secondary combustion chamber. There it serves as supplemental or reburn fuel and an organic source of urea and ammonia (NH3). Upon co-firing manure and coal, NH3 is released from manure and combines with NOx to produce harmless N and water.
Gasification is the process by which carbonaceous fuel (any fossil or biomass fuel consisting of /or containing carbon) is converted to a useable gaseous product without complete combustion of the fuel. The process occurs in an oxygen deficient (partial oxidation) environment at high temperatures (Figure 2). The resulting fuel is a producer gas (a synthesis gas or syngas) that consists primarily of varying ratios of hydrogen and carbon monoxide (CO).
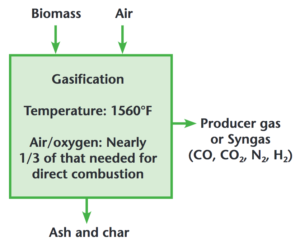
Fig. 2: Biomass gasification process
Syngas can be further processed into other fuels or products by chemical conversion or burned to heat a conventional boiler. Also, it can replace natural gas in a gas turbine.
Pyrolysis is a thermo-chemical conversion process whereby biomass is heated at high temperatures in the complete absence of an oxidant (oxygen). Products for this process include combustible gas, liquid condensates and charcoal. The liquid portion is called pyrolysis oil, which can be burned to generate electrical power. It can also be used as a chemical additive to produce plastics and other bio-products.
On-site Manure to Energy Conversion Systems
Opportunities exist for an on-site or on-farm manure to energy conversion system. Small and modular conversion units could be installed in the facility to eliminate issues associated with transport of manure off site. Animal facility operators could build these systems to process and convert part of their waste streams and to produce auxiliary energy and power, including bio-fuel for farm use. As the operators learn to work these systems, they could add more units and increase the amount of waste stream to process. This would provide them a totally closed-loop system for waste handling.
An example would be a modular anaerobic digestion system. It directs part of the manure stream to a covered lagoon, which acts as an anaerobic digester. Methane that is produced could be cleaned and used to power a small engine-generator set-up to generate electricity. This will satisfy a portion of their power requirement.
The sludge generated from the digester after the digestion process could be used to run an onsite gasification system. Energy from this system can be used for the thermal energy needed for drying sludge that has been previously separated from its watery stream.
Several modules of digester-gasifier combination may be installed, depending on the needs and capability of the facility. As the research community establishes newer technologies for highly advanced systems for liquid fuel production, operators and managers of these combined systems would already have some experience in operating them for on-farm heat and power generation. Simultaneously, they would be reducing potential for animal waste pollution.
Co-Products and Residues
Essentially all bioconversion processes will result in residues that might not have immediate value. For instance, most, if not all, of the plant nutrients will remain following bioconversion or thermo-chemical conversion. However, these nutrients may be in different forms than customarily found in the original bio-energy feedstock.
Challenges ahead will involve finding processes, uses and markets for these co-products. Possibilities may include animal feed, fertilizers, soil conditioners, construction materials or chemical extraction.
Original article by Saqib Mukhtar and Sergio Capareda.
Produced by Agricultural Communications, The Texas A&M University System.
Extension publications can be found on the Web at: http://tcebookstore.org.